Relieving the economic pressures in manufacturing with automated palletizing
The persistent economic challenges facing manufacturing persist with regional inflation, global conflicts, an aging workforce, disruptions in the supply chain, health epidemics, and other compounding factors, each playing a role. Business owners who reassess their strategy and consider automation are ahead of the curve.
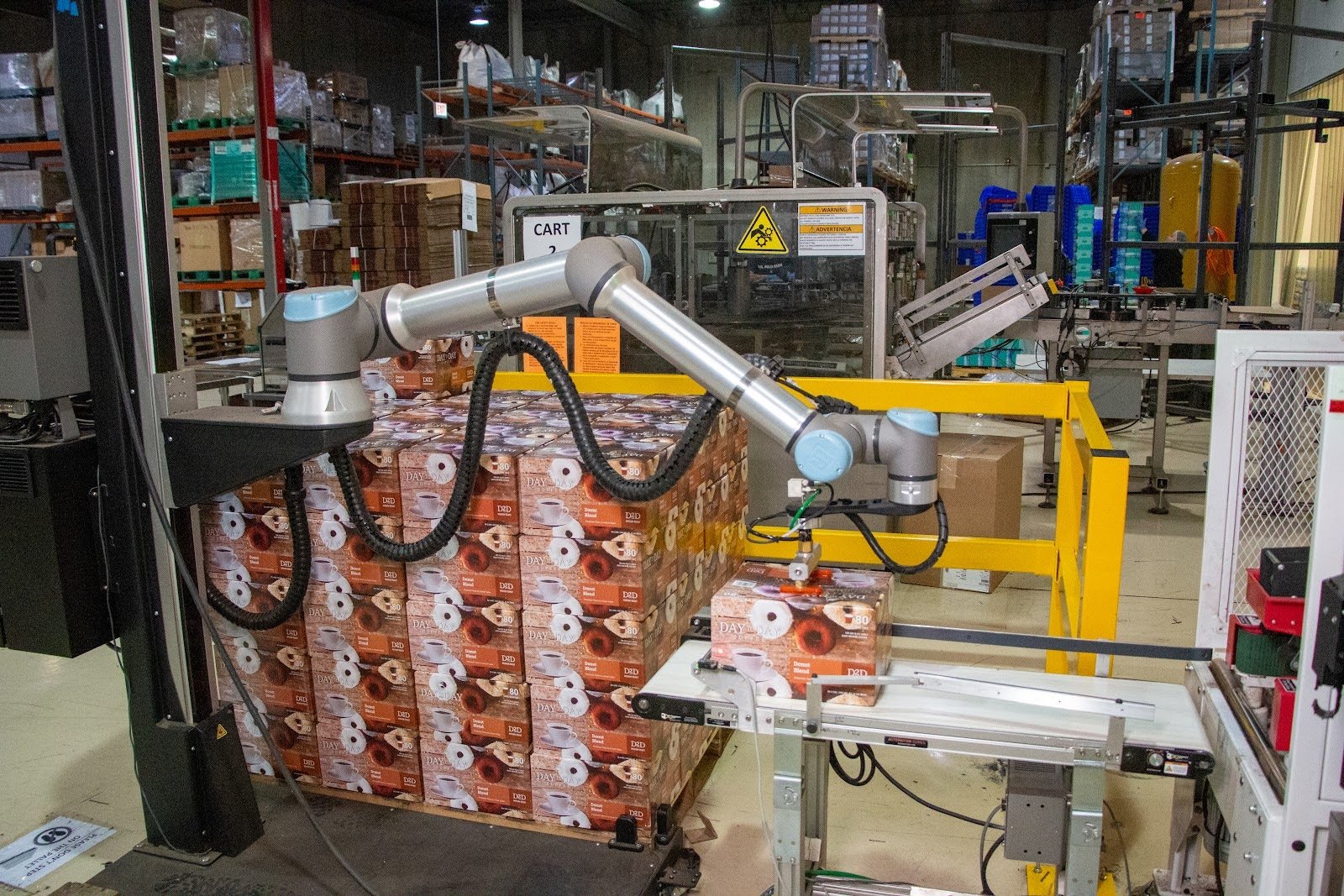
The persistent economic challenges facing manufacturing persist with regional inflation, global conflicts, an aging workforce, disruptions in the supply chain, health epidemics, and other compounding factors, each playing a role. Business owners who reassess their strategy and consider automation are ahead of the curve.
As demonstrated throughout the COVID pandemic, businesses equipped with automation were more resilient to shifts when compared to their counterparts. ASME noted that “investing in automation and robotics was one way companies coped with the loss of workers.” Manual jobs like palletizing were relatively straightforward to fill not long ago. The abundance of available workers, limited e-commerce, and reduced product complexity made conducting business with manual labor possible.
Today, the economic environment is almost entirely different: the available (and interested) workforce is diminishing, e-commerce continues to grow and product diversity is expanding. These headwinds have created a new boom in automation investments, particularly in collaborative robotics. Manufacturers are discovering that cobot palletizers, for example, are more accessible, have a smaller footprint, and are more budget-friendly. This allows them to address people, productivity, and adaptability challenges. This article explores how these automated palletizing systems are becoming vital tools in industries such as food & beverage, consumer goods, and pharmaceutical production.
People: Enhancing workforce dynamics
Automation is doing jobs that people don’t want.
Automation is doing jobs that people don’t want.
A frozen fish producer, Korea Pelagic, needed help finding people to stack pallets of fish in a freezer. Palletizing fish on very tall pallets is a physically demanding undertaking in the cold, making it challenging to find willing workers. There were very few people willing to work this repetitive, monotonous, dangerous job. Time is essential in food production, so Korea Pelagic turned to automation to ensure timely shipments.
A palletizing cobot was the perfect solution for this demanding environment. Not only was the cobot willing to work in the cold, the result was a 200% increase in productivity and an opportunity to provide more rewarding and sustainable work for their employees. Read the complete case study.
Show respect for the workforce.
TIDI Products, a leader in infection prevention and patient safety products, faced inefficiencies due to a shortage of workers. One person did two tasks to keep up with production demands. Overburdening a person slowed down production, increased their backlog, decreased morale, and limited the number of orders TDI Products could accept. TIDI invested in end-of-line automated palletizing systems. This solution addressed operational bottlenecks, decreased ergonomic issues, and increased team job satisfaction.
The palletizers performed better than expected, so TIDI Products acquired two more systems.
Initially, people worried that robots would take their jobs. Now, people expect employers to invest in supporting and helping their employees. This includes making automation take the burden of the manual and repetitive tasks they do not want to do. If employees do not like the job or feel like their employer is not investing in them, they leave. This is more prevalent in younger generations who feel the need to switch jobs to care for their interests.
According to Business Insider, 73% of Gen Z workers are willing to take a pay cut or a lower position if their job does not meet their needs. Gen Z (born between 1997 and 2012) is rejecting monotonous, physically demanding jobs and further shrinking the available labor. As this trend continues, businesses will inevitably need to invest in automation.
Companies must invest in their employees to increase worker retention. TIDI Products Value Stream Manager Cameron Lemke summarizes: “If you’re in a business that cares about your team, this is an easy investment to help them feel supported and encourage their longevity with your business.”
“If you’re in a business that cares about your team, this is an easy investment to help them feel supported and encourage their longevity with your business.” |
Read and watch the TIDI Products case study.
Create sustainable jobs (that people want).
Cascade Coffee, a roasting and co-manufacturing company, experienced chronic labor shortages and safety issues in their manual palletizing operations. With the deployment of automated palletizing units, job satisfaction and safety were improved. The system's adaptability allowed for seamless integration, optimizing productivity and allowing employees to advance. It took 5 minutes to train an operator on the cobot. Now, the palletizer does the lower-paid job, and the people advance in the company. Watch how Cascade Coffee palletizes 6,500 cases a day and grows its employees.
Productivity: Unleashing operational potential
Every pallet counts.
The objective is to prevent unplanned downtime. Although frequently overlooked, the palletization process can emerge as a bottleneck. In a one-piece-flow environment, the cycle time would have to decrease to match the speed of the slowest task. Automation can alleviate this bottleneck and bring cycle time closer to takt time. Cascade Coffee's transition from manual to automated palletizing resolved labor shortages and eliminated bottlenecks.
“The simple manual processes were consuming just an immense amount of time to where machines would stop because operators actually couldn’t palletize fast enough.” – Ron Kane, COO of Cascade Coffee. Watch the full video. |
The cobots ensure a continuous and efficient production flow, allowing for the optimization of resources and fulfillment of delivery deadlines.
Automated palletizing increases throughput.
TIDI Products experienced significant gains in productivity after incorporating automated palletizing units. They documented productivity gains of 30% from the first palletizing cell. Subsequent cells have increased by a similarly impressive 25%. Productivity gains allows manufacturers to optimize resource utilization, reduce production costs, and maintain competitive pricing.
Robotic palletizers also increase productivity in food production. Bread manufacturer Antic in Spain faced difficulties manually palletizing products on two production lines. The company needed a scalable, automated solution to accommodate various product weights and improve production speed. Labor shortages added to the urgency of finding an effective resolution. Their search led them to a palletizing collaborative robot that runs two automated lines and increased production speed by 30%.
An automated system can keep up.
Automated palletizing systems provide high efficiency by keeping up with manufacturing processes. User-friendly software makes it easy to change the palletizing cobot for new box sizes or pallet configurations. For example, the Robotiq Palletizing Solution automatically generates and optimizes trajectories and cobot movements. Robotiq uses assistant tools and simple configurations. Input requirements such as:
- Box dimensions, weight, and orientation
- Pallet dimensions
- Pallet configuration
This software works for the person instead of the person working for it. With a few minutes of training, operators can have the automated palletizer stacking boxes.
Adaptability: Meeting market demands with ease
Be led by customer requirements and market opportunities, not factory limitations.
Despite the economic pressures in manufacturing, every company aims for customer-driven leadership rather than being dictated by external factors. This means factories must remain agile and productive.
Napco, a coffee distribution company, highlights the productivity gains experienced when using palletizing systems. The lead operator, who had no prior experience in robotics, was able to learn how to operate the system quickly. This automated palletizing system created a 15% increase in productivity.
Streamlined expansion: timing your costs with benefits
The flexibility and modular design of automated palletizing solutions enable streamlined expansion. With the ability to replicate and integrate additional units onto different production lines, manufacturers can scale effectively in response to fluctuations in demand. TIDI saw this first hand. Scalability, combined with a typical payback period of one year, ensures a substantial return on investment and positively impacts the bottom line.
Automated palletizing systems with integrated cobots have become indispensable allies for food & beverage, consumer goods, and pharmaceutical manufacturers facing continued economic pressures. These systems help them navigate labor-related challenges, enhance productivity, and foster adaptability.
Control your future
At Robotiq, we follow the principles of LEAN ROBOTICS to create a standardized solution that is easier to scale, repeatable, and easy to use. We understand the economic pressures in manufacturing and we have experience working with food & beverage, consumer goods, and pharmaceutical manufacturers.
Let us get you started - implementation is easier than you think. Discuss with one of our automation experts today to kickstart your project.